Challenges in Vacuum Chamber Design and Manufacturing
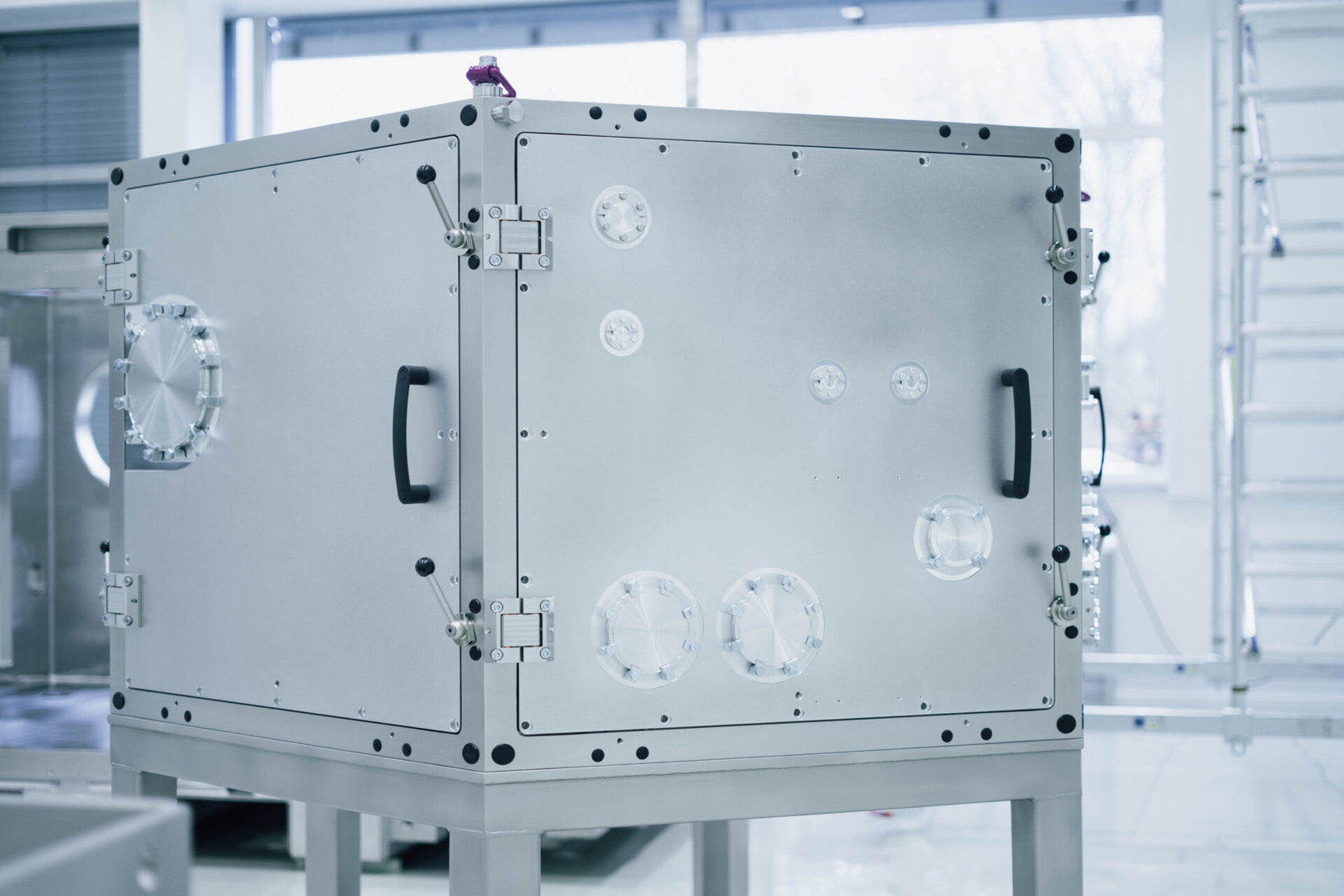
The Construction of vacuum chambers demands a high level of precision and accuracy. To attain the vacuum integrity a slight misalignment or unnecessary tolerance can lead to inappropriate results. The Term “Vacuum integrity” is not just a technicality in vacuum casting services, it is also a fundamental requirement as slight imperfection or misalignment compromises the chamber’s ability to gain a robust vacuum.
To gain this high level of accuracy precision machining is the most important paramount. With the help of advanced multiaxis machining, the engineers can address challenges that are associated with material for the vacuum chambers, sealing mechanisms, structural integrity, pumping systems, temperature control, instrumentation, accessibility, leak detection, compliance with standards, and cost optimization.
Further in this article, we will delve into the challenges of vacuum chamber design and manufacturing. We will figure out how modern machining helps to create these intricate geometries and ensure exact results that meet the international standards of aerospace, scientific, and industrial applications.
Precise Machining of Flanges and Seals in Vacuum Chambers
The precision machining of flanges and seals is the most important paramount in achieving the required vacuum integrity. The flanges play a pivotal role in determining the chamber’s overall efficiency. As the flanges are known as connectors between chamber components, they must be machined so precisely that they create seamless interfaces between the part’s geometry. The machining process for flanges includes cutting, shaping, optimizing, and finishing so that they fit flawlessly and create a hermetic seal when joined.
Material selection for flanges and seals is a very important aspect of ensuring optimum performance in vacuum environments. The commonly use materials are Stainless steel alloys such as ASTM A20, and ASTM A276 which are used because of their corrosion resistance and mechanical strength properties. Some Aluminum alloys such as ASTM b211 or AMS are also used in manufacturing. Copper alloys ASTM B152, and ASTM B370 are used in balancing electrical conductivity.
Similarly, the manufacturing of seals requires a little more accuracy. However, whether you use elastomers, metals, or specialized materials for manufacturing purposes advanced multiaxis machining helps to achieve the desired flexibility and resilience, so that these parts can bear the dynamic load conditions within the chamber.
In the meantime, the surface finish of the flanges is very crucial as it helps prevent leaks in the vacuum system. Ra (average roughness) values are closely observed in manufacturing. Lapping and polishing may also be required to achieve the required surface finish.
Bore and Cylinder Machining for Smooth Pumping Operation
In the manufacturing of vacuum chambers, the bore and the cylinder machining of the pumping system play a very important role in ensuring efficient and smooth operation. Precision machining helps in achieving the precise dimension and the surface finishing in these components is essential for maintaining the desired vacuum levels and maintaining the performance of the vacuum pumps.
One significant challenge overcome by advanced machining is maintaining uniformity in large-scale chambers or intricate geometries as a small deviation can cause uneven pumping pressure or even in some cases cause pump failure.
Honing and lapping processes are very effective in achieving ultra-smooth surfaces in the bore and cylinder machining. The honing technique involves the use of abrasives to increase the smoothness of the surface finish and create precise dimensions.
While lapping use fine abrasive particles for the fine tuning. The bore and the cylinder machining must consider thermal expansion and contraction of the material especially in vacuum chambers where temperature fluctuations can happen significantly. Selecting the material with appropriate thermal conductivity and stability is essential.
To check the precision in measurements, precision measuring instruments such as coordinate measuring machines (CMMs) must be used to ensure the dimensional verification of the bore and cylinder machining. Helium leak testing is a common quality control measure to ensure the absence of leakage in bore and cylinder machining.
Similar Posts
Why Toothpaste from Human Hair Became a Topic in 2025?
Is Wcofun TV the Right Choice for Animated Entertainment? An Unbiased Review
Understanding the Phone Number 0394926347